Facilities available at Robotics and Intelligent Systems Lab
- Rhino Robot XR-1
- PUMA 560 I ROBOT
- Move Master
- SIR-1
- CYTON
- Haptic devices
- NI ELVIS -II, cRIO
- NI CVS with Camera
- NI USB DAQ & PXI
- TEKTRONIX M80
- HP OSCILLOSCOPE
- Sensors for AUV
- PLC
- EV3 & Lego Kits
- Parallax
- CrossBow Sensors
- Workstation
- D Space 1104 kit
- Quanser Q8 kit
Rhino Robot XR-1
DESCRIPTION:A five axis robot arm. Constructed out of 0.125 inch and 0.250 inch thick aluminum plate for years of trouble free service. Powered by six PMDC servo motors with integral gearboxes and incremental encoders. Home position microswitches on all axes and on the hand.
Model | XR-3 Robot Arm |
Applications | Education,training, research |
Configuration | 5 Axes plus gripper All axes completely independent All axes can be controlled simultaneously |
Drives | Six PMDC servo motors with integral gearboxes and incremental optical encoders |
Controller | Mark I controller from Rhino (optional) |
Payload | 2.2 pounds(1 kilograms) |
Speed(Gripper) | 1 second to open; 2 seconds to close |
Speed (Axes) | 40 degrees per second |
Repeatability | 0.157 inches at full extension |
Weight | 16 pounds(7.3 kg) without base; base is 10 pounds (4.5 kg) |
Reach | 24 inches from center of waist to finger tips |
Work Envelope | Motor "F" Body Rotation - 350 degrees Motor "E" Shoulder Rotation - 210 degrees Motor "D" Elbow Rotation - 265 degrees Motor "C" Wrist Rotation - 310 degrees Motor "B" Gripper Rotation - +/- 7 revolutions |
Standard Gripper |
1-1/4 inch
(31.7 mm) opening for position 1 2-1/2 inch (63.5 mm) opening for position 2 |
End Effector Options |
Long finger
attachment Triple finger attachment Narrow finger attachment Clam shell finger attachment Shovel attachment Moto Dremel hand Rhino writer hand Vacuum finger attachment End effector package (includes above) |
Accessories | Rotary carousel Tilting rotary carousel X-Y table Belt conveyor Slide base Experimental motor kits Support hardware kit |
Software for PC | RoboTalk robot control language Kernel control language |
PUMA 560 INDUSTRIAL ROBOT
A robot is a servo controlled manipulator that made various programmed tasks. A robotic arm is the constituted by a kinematic chain which
is a set of rigid bodies (links) attached to articulations (joints) that permit the relative motion between two elements. In the kinematic
chain the links have parameters such as weight, inertia, and size, among others. The joints have features of articulation type and DOF.
The PUMA 560 robot has six links and six DOF (rotary type joints in function of an angle θ). The first three DOF are located in the arm
which allows determining the robot position. The following three DOF's are located in the end effectors to provide orientation,
Figure shows the physical constitution of this model and Table. the extent to which each articulation account.
Figure 1. Links and joints for PUMA 560 structure
Table : Motion limits for six Dof for PUMA 560 Joint Range (degrees)
JOINTs | RANGE(degrees) |
---|---|
1 | -160° – 160° |
2 | -245° – 45° |
3 | -45° – 225° |
4 | -110° – 170° |
5 | -100° – 100° |
6 | -266° – 266° |
DH parameters of Puma 560 manipulator

PUMA 560
MOVE MASTER RM-501
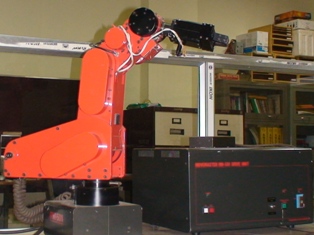
System | Specification | |
---|---|---|
Structure | Five degrees of freedom Vertical multi-joint type | |
Range of Movement | Waist rotation | 300° |
Shoulder rotation | 130° | |
Elbow rotation | 90° | |
Wrist pitch | +/-90° | |
Wrist roll | +/-180° | |
Permissible handling weight | max. 1.2kg(include weight of hand) | |
Maximum synthesis speed | 400mm/sec (wrist tool surface) | |
Position repeat accuracy | +-0.5mm (wrist tool surface) | |
Drive system | Electroservo drive by a DC servomotors |
SIR-1
CYTON Bihanded robot from Energid with Actin Viewer
Phantom Omni Haptic devices
NI ELVIS - II, cRIO
NI ELVIS - II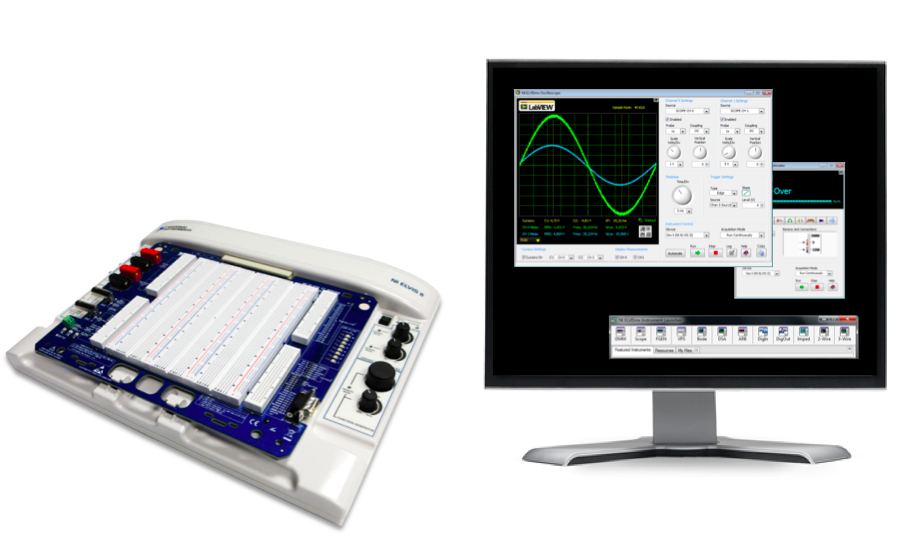
NI ELVIS includes 12 of the most commonly used laboratory instruments in a single hardware platform.
- Oscilloscope
- Digital Multimeter
- Function Generator
- Variable Power Supply
- Dynamic Signal Analyzer
- Bode Analyzer
- 2 Wire Current-Voltage Analyzer
- 3 Wire Current-Voltage Analyzer
- Arbitrary Waveform Generator
- Digital Reader
- Digital Writer
- Impedance Analyzer
The National Instruments cRIO-9002 real-time embedded controllers offers powerful stand-alone embedded execution for deterministic LabVIEW Real-Time applications. The National Instruments cRIO-9002 includes 32 MB of DRAM memory and 64 MB of nonvolatile flash storage for file storage. The National Instruments cRIO-9004 includes 64 MB of DRAM memory and 512 MB of nonvolatile flash storage for data-logging applications. Both controllers are designed for extreme ruggedness, reliability, and low power consumption with dual 9 to 35 VDC supply inputs that deliver isolated power to the CompactRIO chassis/modules and a -40 to 70 °C temperature range. A 195 MHz industrial processor balances low power consumption with powerful real-time floating-point signal processing and analysis capabilities for deterministic control loops exceeding 1 kHz.
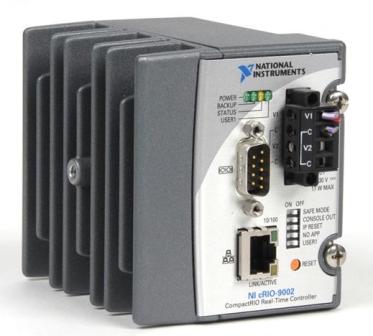
NI CVS - Compact Vision System
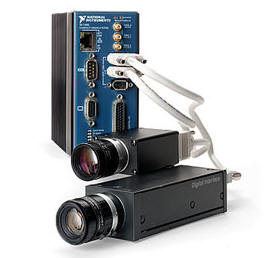
NI USB DAX & PXI
TEKTRONIX M80
HP DIGITAL STORAGE OSCILLOSCOPE
Sensors for AUV
MT9, TCM5, XBOW, PARACSENTIFIC DEPTH SENSOR, DVL, ALTIMETER, MICRON FORWARD LOOKING SONAR
Web PLC from TriLogic
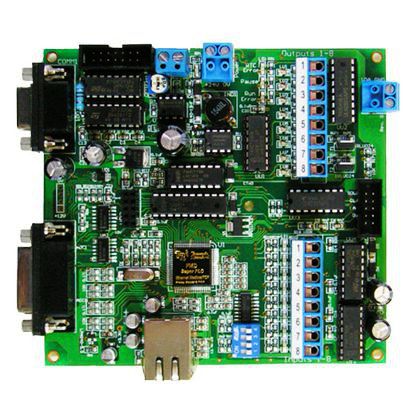
Built into the FMD88-10 PLC are 8 digital inputs (includes 2 high speed encoders, 4 pulse frequency measurement and 4 interrupts), 8 digital outputs (supports 4 PWM channels, 3 stepper motor pulse/direction controls), 8 analog inputs (0-5V, 12-bit) and 2 analog outputs (0-5V or 0-10V, 12-bit). Programming of the FMD88-10 PLC is simplified with powerful i-TRiLOGI Ladder+BASIC software. The FMD88-10 PLC incorporates a program code security feature in the interest of Automation OEMs' program protection.
EV3 & Lego Kits
EV3 Programmable Brick
The EV3 Brick serves as the control center and power station for your robot.
- 4 Input ports: 1, 2, 3, 4 (to connect sensors to EV3 Brick)
- 4 Output ports: A, B, C, D (to connect motors to EV3 Brick)
- 1 Mini USB PC port (to connect EV3 brick to computer)
- USB host port (to add Wi-Fi dongle and do “Daisy chaining”)
- Micro SD Card port (to increase available memory for EV3 Brick)
- Built-in speaker
Parallax
CrossBow Sensors
Workstation SGI octane III
D Space 1104 kit
Quanser Q8 kit