What is a Centrifugal pump?
A centrifugal pump is a rotor dynamic pump that uses a rotating impeller to increase the pressure of a fluid.
1. Rotating impeller of the pump increases the velocity of liquid.
2. When its flow velocity increases, Kinetic energy is added to the liquid which is later converted to pressure energy partly by increasing the flow area of casing (decreases the velocity).
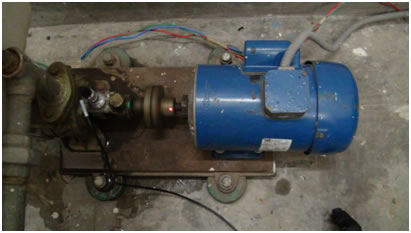
Fig. 1: Centrifugal Pump
Working of Centrifugal pump
1. Liquid is forced into impeller.
2. Vanes pass kinetic energy to liquid:liquid rotates and leaves impeller.
3. Volute casing converts KE to pressure energy.
Fig. 2: Schematic diagram of a centrifugal pump
(Source: Images.google.com)
Advantages of centrifugal pump
Centrifugal pumps are used in a wide variety of applications. These machines operate at high speeds and usually are directly connected to the prime mover (or electric motor) so that the transmission losses are small. There are minimum number of moving parts which reduces the maintenance and increase the working time, other advantages of centrifugal pumps (over reciprocating pump) are smaller size and low installation costs.
Problems faced in centrifugal pump
1. Wear out of impeller.
2. Vibrations
3. Leakage along shaft
4. Bearing failure
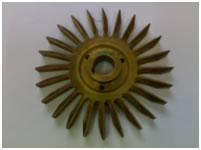
Fig3: Normal impellers
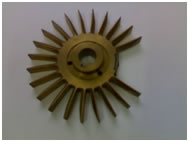
Fig 4: Defective impellers(Broken vanes)
Various condition monitoring techniques have been developed for determining the health and condition of the equipments and machineries like:
1. Temperature monitoring
2. Noise monitoring
3. Debris monitoring
4. Leakage monitoring
5. Vibration monitoring
6. Motor current signal analysis
Out of all these techniques, vibration monitoring and MCSA are most suitable for detection of faults in centrifugal pumps. Hence these two techniques have been used in this experiment to detect the faults for different types of impellers.
Vibration Monitoring
It normally consists of vibration measurement, data collection and data analysis. It is basically monitoring the response of the system or machine to internal & external forces being applied. The response is measured by a transducer (like accelerometer) at the pump and motor bearings and is passed through data cable to the analyzer for interpretation. Vibration transducer transforms the vibrating motion (displacement, velocity, acceleration) to electrical signal form.
Motor current monitoring
It is a technique used for analysis of dynamic and energized system. It is an online/offline analysis technique which includes instantaneous current measurement, FFT of current, etc. to detect fault in motor driven machinery while it is operating. It uses Hall Effect sensor (as a transducer) and analyzer for analysis. By this analysis the faults (like broken rotor bars, bent shaft, bearing irregularities etc) can be detected.